Digitalization Simplifies the Collection and Monitoring of Energy Data
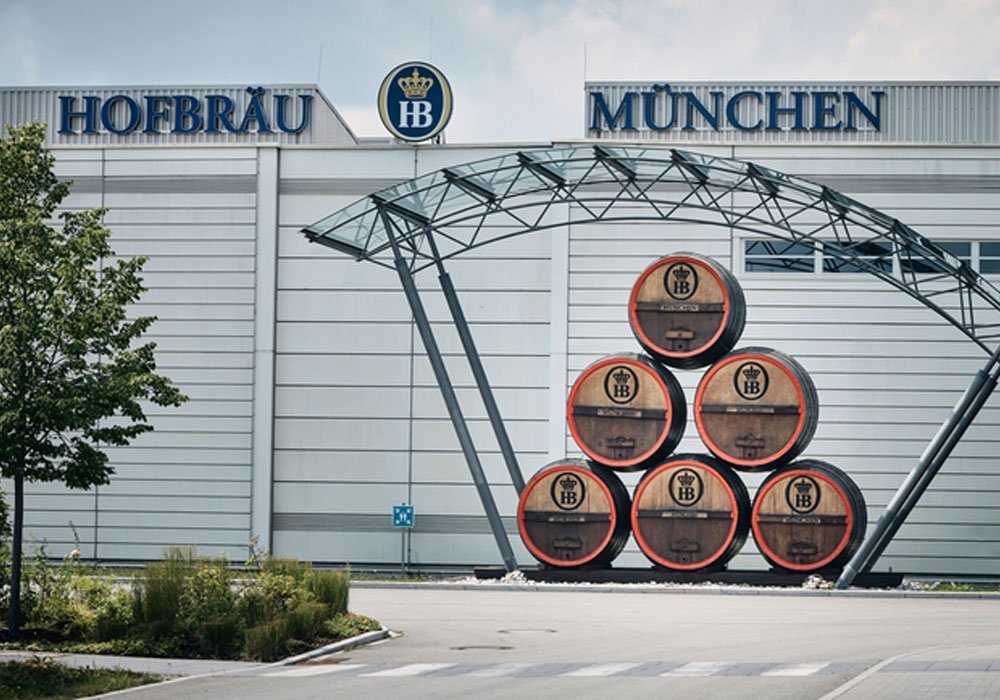
In a world where everybody is trying to find ways to save energy and reduce their carbon footprint, understanding where and how you can make a difference is critical. As you might’ve guessed, brewing beer utilises lots of energy, water and produces a substantial amount of carbon. But that doesn’t mean significant energy savings cannot be found within the brewhouse. Many breweries are funnelling major investments into meeting global sustainability standards through renewable energy and heat recovery initiatives. It is always essential to track and analyse the data to monitor the energy consumption. Digitalization simplifies the collection and monitoring of energy data.
For a brewery to realise and understand their savings potential in terms of equipment utilisation and align with their environmental goals, it is crucial to adopt to the energy monitoring systems which serves as a solution to all problems. Hofbräuhaus is the first German brewery to analyse its own climate emissions. Their goal was to decrease the specific heat consumption by 4 percent and production-generated CO2 emissions by as much as 30 percent. To reach this goal, an automation concept for the integration of data had to be developed to ensure there’s a seamless collection of energy utilisation data.
With the support and expertise of Endress+Hauser and thanks to digitization, monitoring was simply integrated into the existing infrastructure of Hofbräuhaus and mobile access to the data was also available.
Offerings by Endress+Hauser for Energy Monitoring 4.0
Memograph M
The heart of the solution is the Memograph M by Endress+Hauser, a data manager that serves as an interface between the field instruments and the process control level by supporting all common field buses. The Memograph M forwards the actual sensor measurement values to the control system via PROFINET. Thanks to its mathematical functions, Memograph M can directly calculate the amount of heat, which it then sends to the software platform via Ethernet TCP/IP.
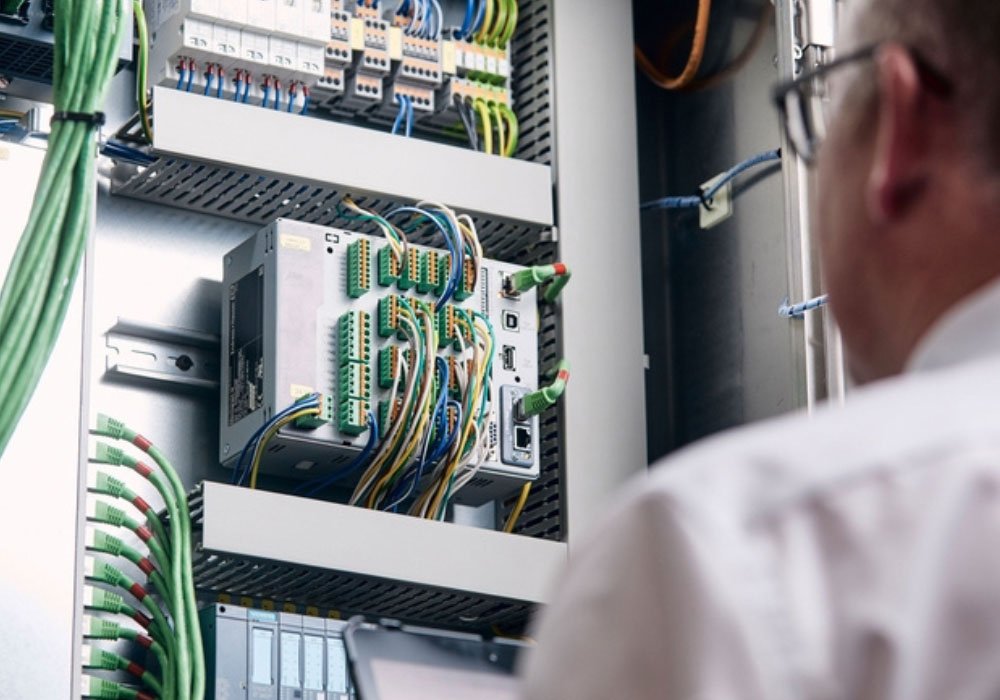
The integrated web server gives operators remote access at the field instrument level and provides a convenient way to configure parameters or store data. Memograph M is the simplest, most cost-effective solution for data integration and energy metering.
Field Xpert
Mobile access to the energy data monitoring system is fulfilled by the FieldXpert. This robust industry-scale tablet PC features a pre-installed device driver library for all important protocols and automatically detects instruments with a click and connects to all Endress+Hauser instruments via WLAN or Bluetooth. That means it can be used to track energy utilisation from anywhere on the grounds of the plant, display trends or launch error analyses. With the FieldXpert, operators can track energy utilisation or launch error analyses from anywhere.
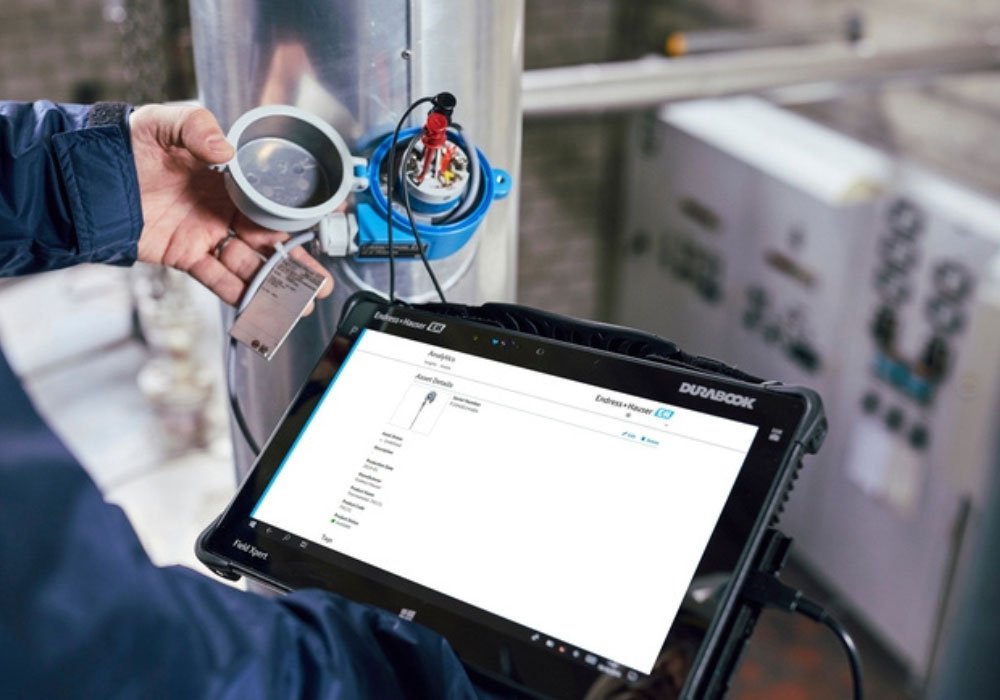
“With the FieldXpert I have simple and fast mobile access to the current energy utilisation data from anywhere, plus I can analyse trends and configure the instruments. Combined with the Memograph, we can exploit the advantages of digitalization down to the field instrument level.” – Silvio Di Tano, Head of Electronics, Staatliches Hofbräuhaus München.
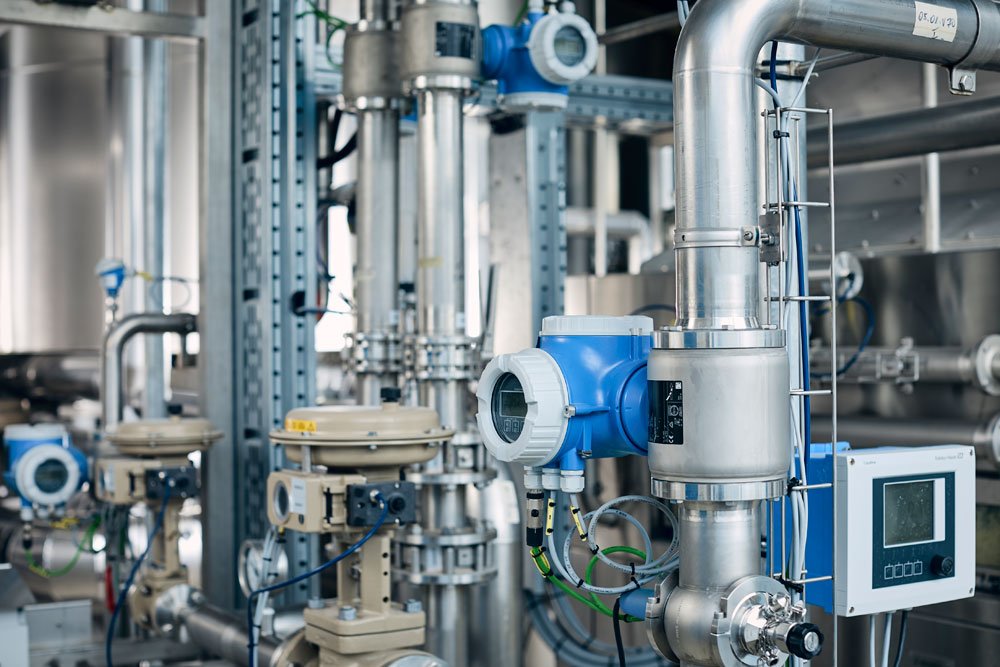
Regardless of the product, continuous monitoring ensures fully transparent energy utilisation, from brewing to filling. Thanks to digitization, monitoring was simply integrated into the existing infrastructure. State-owned Hofbräuhaus is thus in a good position to stake its claim as a role model when it comes to both climate protection and digitalization.
For further information, please reach out to marcomm.in.sc@endress.com